Plywood är tillverkad av tre eller flera tunna lager trä som limmas samman med ett lim. Varje lager trä, eller plywood, är vanligtvis orienterat med sin ådring i rät vinkel mot det intilliggande lagret för att minska krympningen och förbättra styrkan hos det färdiga stycket. De flesta plywoodbitar pressas till stora, plana ark som används i byggnadskonstruktioner. Andra plywoodbitar kan formas till enkla eller sammansatta kurvor för användning i möbler, båtar och flygplan.
Användningen av tunna trälager som konstruktionsmedel dateras till ungefär 1500 f.Kr. då egyptiska hantverkare limmade tunna bitar av mörkt ebenholtsträ på utsidan av en cederkista som hittades i kung Tut-Ankh-Amons grav. Denna teknik användes senare av grekerna och romarna för att tillverka fina möbler och andra dekorativa föremål. På 1600-talet blev konsten att dekorera möbler med tunna träbitar känd som fanering, och själva bitarna blev kända som faner.
Fram till slutet av 1700-talet skars fanerbitarna helt för hand. År 1797 ansökte engelsmannen Sir Samuel Bentham om patent som omfattade flera maskiner för att tillverka faner. I sina patentansökningar beskrev han konceptet att laminera flera lager faner med lim för att bilda ett tjockare stycke – den första beskrivningen av det vi nu kallar plywood.
Trots denna utveckling tog det nästan ytterligare hundra år innan laminerade faner fann kommersiella användningsområden utanför möbelindustrin. Omkring 1890 användes laminerat trä för första gången för att bygga dörrar. Allt eftersom efterfrågan ökade började flera företag producera skivor av flerskiktat laminerat trä, inte bara för dörrar, utan även för användning i järnvägsvagnar, bussar och flygplan. Trots denna ökade användning skapade konceptet att använda "klistrade träslag", som vissa hantverkare sarkastiskt kallade det, en negativ bild av produkten. För att motverka denna bild möttes tillverkarna av laminerat trä och bestämde sig slutligen för termen "plywood" för att beskriva det nya materialet.
År 1928 introducerades de första plywoodskivorna i standardstorlek, 1,2 m x 2,4 m, i USA för användning som ett allmänt byggmaterial. Under de följande decennierna möjliggjorde förbättrade lim och nya produktionsmetoder att plywood kunde användas för en mängd olika tillämpningar. Idag har plywood ersatt sågat virke för många byggnadsändamål, och plywoodtillverkning har blivit en global industri värd flera miljarder dollar.
De yttre lagren av plywood kallas framsida respektive baksida. Framsidan är den yta som ska användas eller synas, medan baksidan förblir oanvänd eller dold. Mittlagret kallas kärnan. I plywood med fem eller fler lager kallas mellanlagren för tvärband.
Plywood kan tillverkas av lövträd, barrträd eller en kombination av de två. Några vanliga lövträd inkluderar ask, lönn, mahogny, ek och teak. Det vanligaste barrträdet som används för att tillverka plywood i USA är Douglasgran, även om flera sorter av tall, cederträ, gran och redwood också används.
Kompositplywood har en kärna gjord av spånskiva eller massiva virkesbitar som sammanfogats kant i kant. Den är ytbehandlad med en plywoodfanér på fram- och baksidan. Kompositplywood används där mycket tjocka skivor behövs.
Vilken typ av lim som används för att binda samman trälagren beror på den specifika tillämpningen av den färdiga plywooden. Barrplywoodskivor avsedda för installation på utsidan av en konstruktion använder vanligtvis ett fenolformaldehydharts som lim på grund av dess utmärkta styrka och fuktbeständighet. Barrplywoodskivor avsedda för installation på insidan av en konstruktion kan använda ett blodprotein- eller sojabönproteinlim, även om de flesta barrplywoodskivor för inomhusbruk nu är tillverkade med samma fenolformaldehydharts som används för utvändiga skivor. Hårdplywood som används för inomhusbruk och vid möbeltillverkning är vanligtvis tillverkad med ett ureaformaldehydharts.
Vissa tillämpningar kräver plywoodskivor som har ett tunt lager av plast, metall eller hartsimpregnerat papper eller tyg limmat på antingen framsidan eller baksidan (eller båda) för att ge ytterytan ytterligare motståndskraft mot fukt och nötning eller för att förbättra dess färghållande egenskaper. Sådan plywood kallas överlagrad plywood och används ofta inom bygg-, transport- och jordbruksindustrin.
Andra plywoodskivor kan beläggas med en flytande bets för att ge ytorna ett färdigt utseende, eller behandlas med olika kemikalier för att förbättra plywoodens flamskydd eller motståndskraft mot röta.
Det finns två breda klasser av plywood, var och en med sitt eget graderingssystem.
En klass är känd som bygg- och industriplywood. Kryssfiner i denna klass används främst för sin styrka och klassificeras efter sin exponeringsförmåga och vilken typ av faner som används på fram- och baksidan. Exponeringsförmågan kan vara inomhus eller utomhus, beroende på vilken typ av lim det används. Fanerkvaliteter kan vara N, A, B, C eller D. N-kvalitet har mycket få ytdefekter, medan D-kvalitet kan ha många kvistar och sprickor. Till exempel är plywood som används för undergolv i ett hus klassad som "Inomhus CD". Det betyder att den har en C-yta med en D-baksida, och limmet är lämpligt för användning i skyddade platser. De inre lagren i all bygg- och industriplywood är tillverkade av faner av klass C eller D, oavsett klassificering.
Den andra klassen av plywood är känd som lövträ och dekorativ plywood. Plywood i denna klass används främst för sitt utseende och graderas i fallande ordning efter fuktbeständighet som teknisk (utomhus), typ I (utomhus), typ II (inomhus) och typ III (inomhus). Deras ytfasader är praktiskt taget fria från defekter.
Storlekar
Plywoodskivor varierar i tjocklek från 1,6 mm (0,06 tum) till 76 mm (3,0 tum). De vanligaste tjocklekarna ligger i intervallet 6,4 mm (0,25 tum) till 19,0 mm (0,75 tum). Även om kärnan, tvärbanden och fram- och baksidan av en plywoodskiva kan vara gjorda av faner av olika tjocklek, måste tjockleken på varje skiva balanseras runt mitten. Till exempel måste fram- och baksidan vara lika tjocka. Likaså måste de övre och nedre tvärbanden vara lika tjocka.
Den vanligaste storleken på plywoodskivor som används i byggnadskonstruktioner är 1,2 m breda och 2,4 m långa. Andra vanliga bredder är 0,9 m och 1,5 m. Längderna varierar från 2,4 m till 3,6 m i steg om 0,3 m. Speciella tillämpningar, som båtbyggnation, kan kräva större skivor.
Träden som används för att tillverka plywood är generellt mindre i diameter än de som används för att tillverka virke. I de flesta fall har de planterats och odlats i områden som ägs av plywoodföretaget. Dessa områden sköts noggrant för att maximera trädtillväxten och minimera skador från insekter eller bränder.
Här är en typisk sekvens av operationer för att bearbeta träd till standardplywoodskivor på 1,2 x 2,4 m (4 x 8 fot):
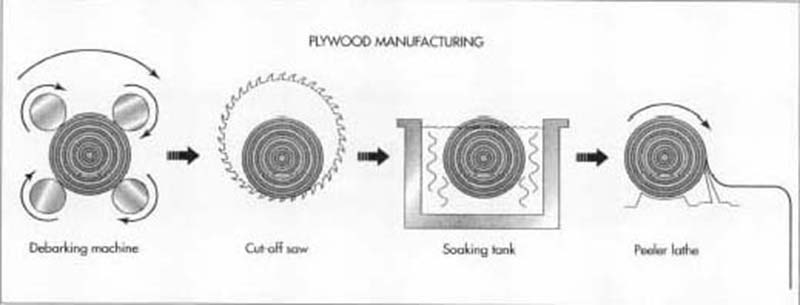
Stockarna barkas först och skärs sedan till skalblock. För att skära blocken till fanerremsor blötläggs de först och skalas sedan till remsor.
1 Utvalda träd i ett område markeras som redo att huggas ner eller fällas. Fällningen kan göras med bensindrivna motorsågar eller med stora hydrauliska saxar monterade på framsidan av hjulfordon som kallas fällare. Grenar avlägsnas från de fallna träden med motorsågar.
2 De beskurna trädstammarna, eller stockarna, släpas till en lastplats med hjulfordon som kallas lunnare. Stockarna kapas till rätt längd och lastas på lastbilar för resan till plywoodfabriken, där de staplas i långa högar som kallas stockdäck.
3 Allt eftersom stockar behövs plockas de upp från stockdäcken av gummihjulslastare och placeras på en kedjetransportör som transporterar dem till barkningsmaskinen. Denna maskin avlägsnar barken, antingen med vasstandade slipskivor eller med högtrycksvattenstrålar, medan stocken långsamt roteras kring sin längdaxel.
4 De barkade stockarna transporteras in i kvarnen på en kedjetransportör där en enorm cirkelsåg skär dem i sektioner som är cirka 2,5 m till 2,6 m långa, lämpliga för att tillverka standardark som är 2,4 m långa. Dessa stocksektioner kallas skalblock.
5 Innan fanern kan skäras måste skalblocken värmas upp och blötläggas för att mjukgöra träet. Blocken kan ångkokas eller doppas i varmt vatten. Denna process tar 12–40 timmar beroende på träslag, blockets diameter och andra faktorer.
6 De uppvärmda skalblocken transporteras sedan till skalarsvarven, där de automatiskt justeras och matas in i svarven ett i taget. När svarven roterar blocket snabbt kring sin längdaxel skalar ett knivblad i full längd ett kontinuerligt fanerark från spinnblockets yta med en hastighet av 90–240 m/min. När blockets diameter minskas till cirka 230–305 mm matas den återstående träbiten, känd som skalarkärnan, ut ur svarven och ett nytt skalblock matas på plats.
7 Den långa fanerarken som kommer ut från/svarven kan bearbetas omedelbart, eller så kan den förvaras i långa brickor med flera nivåer eller lindas på rullar. I vilket fall som helst innebär nästa process att faneren skärs i användbara bredder, vanligtvis cirka 1,4 m, för att tillverka standardplywoodskivor med en bredd på 1,2 m. Samtidigt letar optiska skannrar efter sektioner med oacceptabla defekter, och dessa klipps ut, vilket lämnar kvar fanerbitar med mindre bredd än standard.
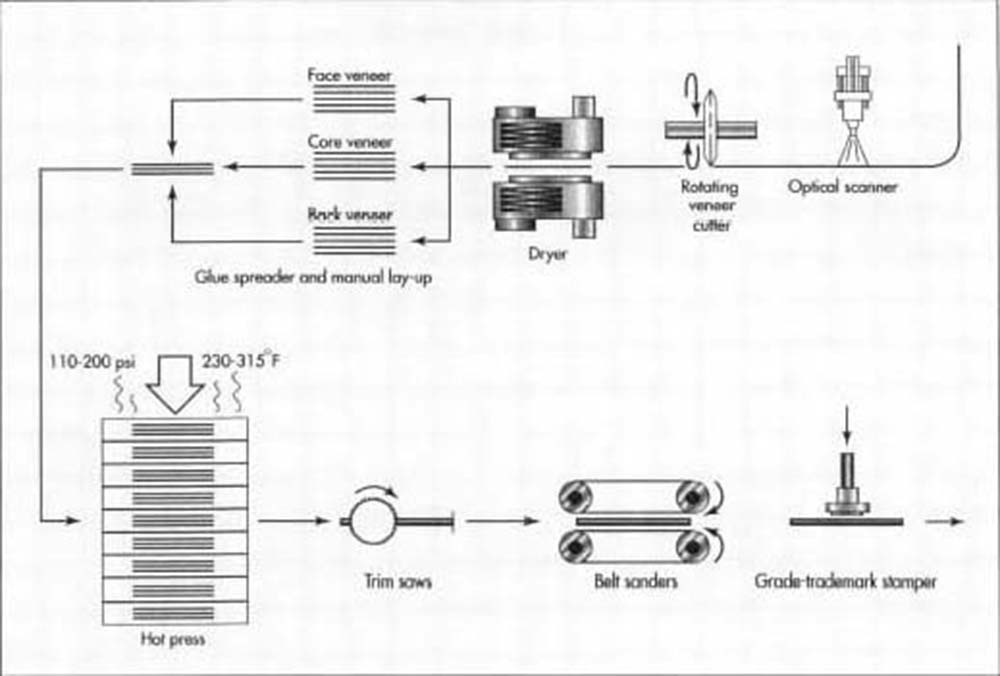
De våta fanerremsorna lindas till en rulle, medan en optisk skanner upptäcker eventuella oacceptabla defekter i träet. När faneret har torkat graderas och staplas det. Utvalda sektioner av faneret limmas ihop. En varmpress används för att försegla faneret till en enda solid plywoodbit, som sedan trimmas och slipas innan den stansas med lämplig sort.
8 Fanersektionerna sorteras och staplas sedan efter kvalitet. Detta kan göras manuellt eller automatiskt med hjälp av optiska skannrar.
9 De sorterade sektionerna matas in i en torktumlare för att minska deras fukthalt och låta dem krympa innan de limmas ihop. De flesta plywoodfabriker använder en mekanisk torktumlare där bitarna kontinuerligt rör sig genom en uppvärmd kammare. I vissa torktumlare blåses strålar av höghastighets, uppvärmd luft över bitarnas yta för att påskynda torkningsprocessen.
10 Allt eftersom fanersektionerna kommer ut ur torktumlaren staplas de efter kvalitet. Sektionerna under bredden har ytterligare faner som skarvas på med tejp eller lim för att göra delarna lämpliga för användning i de inre lagren där utseende och styrka är mindre viktiga.
11 De fanersektioner som ska installeras tvärs – kärnan i treskiktsark eller tvärbanden i femskiktsark – skärs i längder på cirka 1,3 m.
12 När lämpliga fanersektioner är monterade för en viss sträng plywood, börjar processen att lägga upp och limma ihop delarna. Detta kan göras manuellt eller halvautomatiskt med maskiner. I det enklaste fallet med treskiktsskivor läggs baksidans faner platt och körs genom en limspridare, som applicerar ett lager lim på den övre ytan. De korta sektionerna av kärnfaner läggs sedan tvärs över den limmade baksidan, och hela arket körs genom limspridaren en andra gång. Slutligen läggs framsidans faner ovanpå den limmade kärnan, och arket staplas med andra ark som väntar på att gå in i pressen.
13 De limmade arken laddas i en varmpress med flera öppningar. Pressarna kan hantera 20–40 ark åt gången, där varje ark laddas i en separat springa. När alla ark är laddade pressar pressen ihop dem under ett tryck på cirka 7,6–13,8 bar (110–200 psi), samtidigt som de värms upp till en temperatur på cirka 109,9–157,2 °C (230–315 °F). Trycket säkerställer god kontakt mellan fanerlagren, och värmen gör att limmet härdar ordentligt för maximal styrka. Efter en period på 2–7 minuter öppnas pressen och arken tas ut.
14 De grova plåtarna passerar sedan genom en uppsättning sågar, som trimmar dem till sin slutliga bredd och längd. Plåtar av högre kvalitet passerar genom en uppsättning 1,2 m breda bandslipmaskiner, som slipar både fram- och baksidan. Plåtar av mellankvalitet punktslipas manuellt för att rengöra ojämna områden. Vissa plåtar körs genom en uppsättning cirkelsågblad, som skär grunda spår i framsidan för att ge plywooden ett texturerat utseende. Efter en slutlig inspektion repareras eventuella kvarvarande defekter.
15 De färdiga arken stämplas med ett kvalitetsmärke som ger köparen information om exponeringsklassificering, kvalitet, valsnummer och andra faktorer. Ark av samma kvalitetsmärke spänns ihop i staplar och flyttas till lagret i väntan på leverans.
Precis som med virke finns det inget perfekt plywoodstycke. Alla plywoodbitar har ett visst antal defekter. Antalet och placeringen av dessa defekter avgör plywoodkvaliteten. Standarder för bygg- och industriplywood definieras av produktstandard PS1 utarbetad av National Bureau of Standards och American Plywood Association. Standarder för lövträ och dekorativ plywood definieras av ANSIIHPMA HP utarbetad av American National Standards Institute och Hardwood Plywood Manufacturers' Association. Dessa standarder fastställer inte bara graderingssystemen för plywood, utan specificerar även konstruktions-, prestanda- och tillämpningskriterier.
Även om plywood utnyttjar träd ganska effektivt – i huvudsak genom att ta isär dem och sätta ihop dem igen till en starkare och mer användbar konfiguration – finns det fortfarande avsevärt spill i tillverkningsprocessen. I de flesta fall omvandlas endast cirka 50–75 % av den användbara volymen trä i ett träd till plywood. För att förbättra denna siffra är flera nya produkter under utveckling.
En ny produkt kallas orienterad spännskiva, som tillverkas genom att strimla hela stocken i trådar, istället för att skala av ett faner från stocken och kasta kärnan. Trådarna blandas med ett lim och komprimeras till lager med ådringen i en riktning. Dessa komprimerade lager orienteras sedan i rät vinkel mot varandra, som plywood, och limmas samman. Orienterad spännskiva är lika stark som plywood och kostar något mindre.
Publiceringstid: 10 augusti 2021